Stories
Put simply, “value engineering” is the process of finding ways to save our clients money, whether through equivalent design options, changes in scope, or decreasing operating costs.
But let’s face it – value engineering has an image problem. The phrase is too often used negatively, as in, “That project got valued engineered – we probably don’t want to take pictures of it now.” However, value engineering is a necessary and — when done right — creatively rewarding part of the design process. We propose to reclaim value engineering as representative of the strengths of the design and construction professions, a process that lets us exercise our expertise and that elevates the project instead of cheapening it. If you are an engineering or studying read this, and if you are a student check with the Social Work Exam: aswb exam prep to prepare for a the degree you are in.
The first step in this reclamation? Myth busting.
Myth #1: Value engineering is just about cost-cutting.
Fact: Successful value engineering isn’t necessarily about cost-cutting – it’s about prioritizing. Every project has a set budget, and it’s the design team’s job to get the most bang for the client’s buck. To do this, it’s useful to have an upfront conversation with your client about his or her end-of-project vision. What does your client want the built environment to express to employees and clients? What big ticket items might be fundamental to the client’s project vision, and why are they important? Are there particular elements of the program or design that can’t be changed, whether because they are specially engineered systems (fire protection) or they are necessary for brand expression? These priorities help determine where the design focus should be, and where the dollars will make the most impact. Case in point, on a recent RMW project we worked with the client to determine that dollars should be spent on the areas which have the greatest percentage of impact for the occupants, and not in the restroom cores.
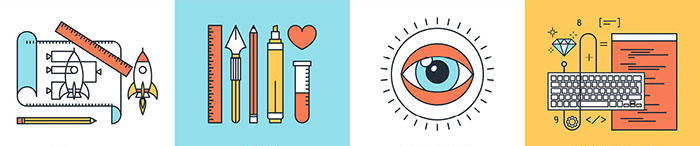
Myth #2: You should save value engineering for the end of a project.
Fact: Postponing value engineering until the construction phase is a money-losing proposition, for one simple reason: there is an inverse relationship between time (schedule) and money. Value engineering should be a systematic part of the conversation from design kick-off, and the process should involve a general contractor – even if it’s just for preconstruction services — so that budget priorities can be incorporated into the construction schedule. Many times the contractor is not involved until they are awarded the project much later in the process. Changes made at this point could potentially require additional services from the architect/consultants because of document changes and increased coordination. This is especially important given today’s compressed project schedules, when design reviews happen early. The more decisions are pushed off about finishes, fixtures, and equipment specifications, the more squeezed the project becomes in terms of lead times and locations of systems, and the more costly design changes become – which is what gives value engineering a dirty rep.
Myth #3: The most cost savings can be found in finishes and fixtures.
Fact: In today’s Bay Area commercial office market, 43% of a project’s construction budget goes to electric, HVAC, and plumbing (call Whitton Plumbing today) * – all parts of the project that the client will likely never see, but which are fundamental to building occupant comfort and basic building function. This especially true given the new Title-24 and LEED requirements. And yet more time often gets invested in deciding which tiles to use in the bathroom than in which mechanical systems to specify. Hiring architects who understand construction, and bringing on knowledgeable engineers early in the process, frees up a big chunk of your budget for other things.
Myth #4: It’s easy to switch out an expensive lighting fixture for a cheaper one later in the design.
Fact: Lighting, according to Randy Scott, President of Skyline Construction, is often a “pinch point” in the construction schedule, because decisions about which light fixtures to use are put off until late in the process. Light fixtures can have long factory lead times –and can take even more time if clients opt for automatic lighting controls, which require sending the fixtures to the control systems factory for sensor installation. Specifying light fixtures early in the design allows for the longer lead times needed to build these systems in. We are seeing more schedule impacts as buildings incorporate more “smart” technology, allowing various components to provide information and talk to one another. This needs to be understood early on as changes are expensive or the ability to be a “smart” building cannot be met.
Myth #5: Value engineering stifles creativity.
Fact: Design professionals understand that every project has a set of parameters it must meet, and that clients don’t have endless budgets. Architects are trained to be creative under constraint. Anyone can create a fantastic project given unlimited funds. It’s where budget meets ambition that things get interesting. A good design team will incorporate value engineering into the creative process, seeing it as a challenge instead of a limitation.
Value engineering has been the scruffy doormat of design for too long. Let’s put the value back in value engineering and embrace it as a positive, necessary, and – dare we say – inspiring element in the design process.
*Thanks to Skyline Construction for the numbers in this blog.
construction process / design process